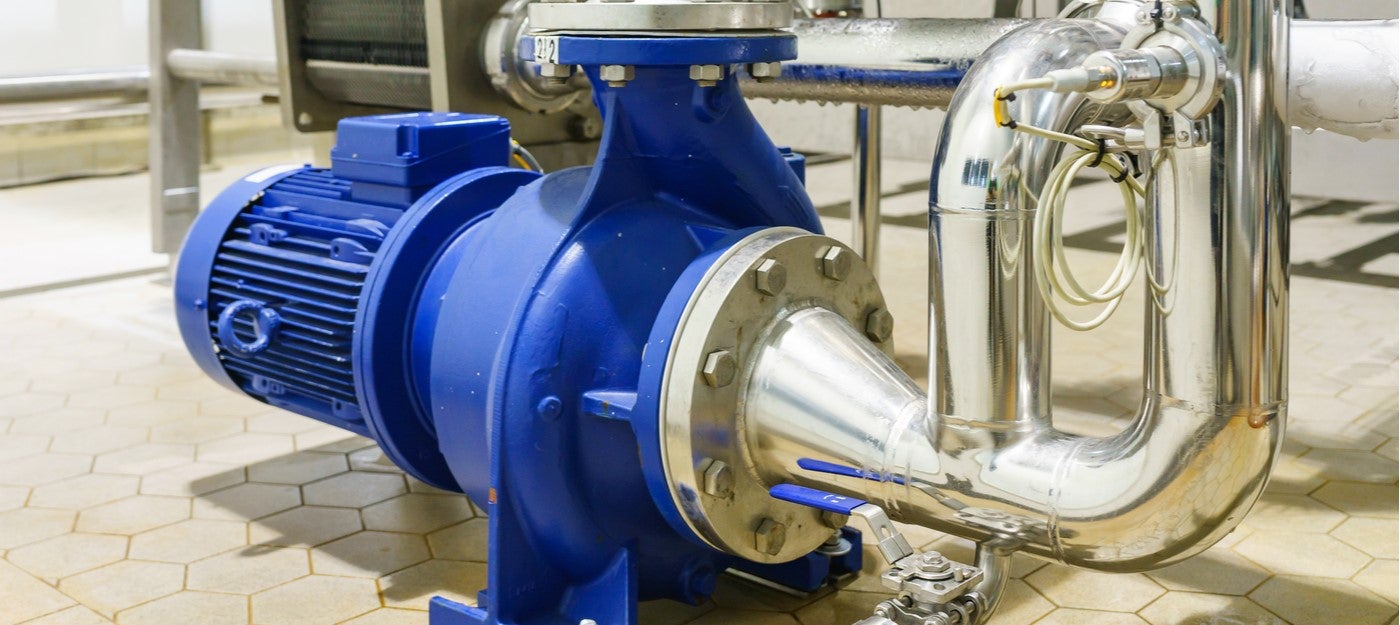
Selecting the mining pump one for a specific mining application can be challenging. The key is to match pump design and materials with the demands of the job (such as flow rates, pressures, and especially the nature of the material being moved)
What mining applications are pumps used for?
In mining, pumps are typically used for:
Dewatering: Removing groundwater or rainwater from pits, tunnels, or shafts.
Slurry transport: Moving a mixture of solids and liquids, often with abrasive particles.
Tailings management: Handling waste materials after ore processing.
Water supply: Delivering fresh or process water to different areas of the site.
What are the different types of mining pumps?
Centrifugal Pumps
These pumps use a rotating impeller to move fluid, making them ideal for high-flow, low-viscosity applications. They’re widely used for dewatering open pits and underground shafts, transporting relatively low-solid-content slurry, and general water transfer around the site.
However, centrifugal pumps can suffer from rapid wear if handling highly abrasive slurry unless fitted with wear-resistant liners and impellers.
Positive Displacement Pumps
These pumps move fluid by trapping a fixed amount and forcing it through the discharge pipe. Common designs include piston, diaphragm, and peristaltic pumps. They’re better suited for high-viscosity fluids, applications requiring precise flow control, and high-pressure slurry transfer.
Positive displacement pumps handle thicker, denser slurries better than centrifugal pumps but may have lower maximum flow rates.
Submersible Pumps
Designed to operate while fully submerged, these pumps are common in dewatering applications where space is limited or suction lift is impractical. They’re often portable, making them ideal for temporary or emergency pumping needs. Submersibles can handle both clean water and slurry, depending on the impeller and housing design.
Mining Pump Manufacturers
As experts in mining equipment, Carroll Technologies has done the research for you.
SAMOA serves the Air-Operated Double-Diaphragm (AODD) pump market. SAMOA’s Pivot UP introduces a unique frictionless Pivot-Shaft Air Valve to provide maximum performance and energy efficiency, which exceeds market expectations.
Equipment Pro can supply rugged pump solutions for any mining application. Among its portfolio is the Equipment Pro no-seal pump, which is designed as a unique bypass/pressure break area and slinger that confines leakage to the area below the discharge head.
Other mining tunneling and water industry pump manufacturers include Mefcor, which supplies simple, clog-resistant industrial pumps for difficult dewatering applications. As its nylon-bristled drive wheel taps do not require a power source, running costs and maintenance are minimal.
You can also find a wide range of pumps from Stancor, who have been industry-leading specialists for over 35 years.
Customized Solutions from Your Pump Distributor
Finding the right pump is not a simple “add to basket purchase”, so Carroll Technologies supports its customers to find the right product, whether it involves a simple application or a fully customized pump network.
Carroll provides a comprehensive range of pump-turbine systems in various models for different situations around industrial facilities.
This includes free-floating pumps and automatic pumps that are used for anything from small amounts of water to large volumes of water such as ponds and flooding issues, both on the surface or underground.