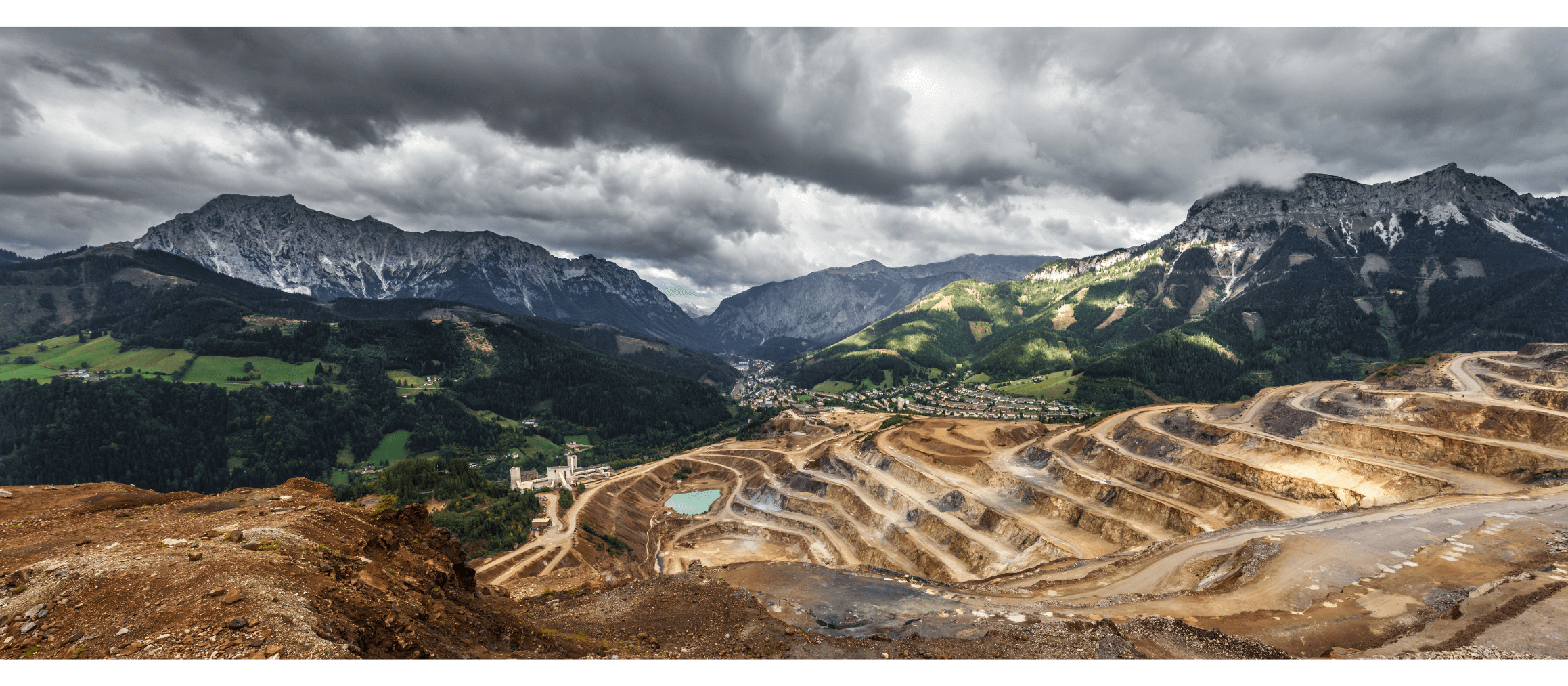
Hard rock mining produces most of the world’s gold, and the US (the fourth-largest gold-producing nation after China, Australia and Russia), produced 200 tonnes of gold in 2019. Mines that produce gold are situated all over the US, with most of the nation’s gold being produced in the state of Nevada. This means that there is a lot of equipment in circulation used for gold mining, from safety equipment to communication solutions to heavy vehicles.
Gold mining equipment
So, what equipment do you need for gold mining? Mines require hoists and conveyor belts (as well as other transport/removal equipment), solutions for ground support (such as bolts), ventilation systems to clear and control hazardous gases and dust, cap lights and visibility solutions, communication networks (such as fixed phones or portable radios), PPE equipment (such as personal gas detectors), and collision avoidance systems for both vehicles/equipment and personnel.
Where to buy gold mining equipment
With such diversity in equipment, having onsite expertise in all areas at all times can be tricky. Finding a trusted distributor who has searched the market for the best solutions for each application is the best way to ensure optimal safety, productivity and profitability.
Carroll Technologies offers safety, communication, motor controls, monitoring, collision avoidance and other gold mining equipment (along with installation and repair services) to mines across the US. With more than 40 years of experience, Carroll only supplies gold mining equipment from the best and most trusted manufacturers on the market.
Gold mining equipment manufacturers
Northern Light Technologies (NLT) has paved the way with cap lamp innovation, incorporating proximity and tracking tags into its world-leading and fully customizable cap light solutions, including NLT Polaris, Rebel and Genesis cap lights.
PBE’s PAS-ZR is a ruggedized version of its standard collision avoidance system, specifically designed for the mining industry. This tag-based detection system can be used for both mobile and fixed assets, including workers, and uses multiple detection technologies simultaneously to provide reliable results. PBE’s MineBoss 2.0 is a centralized control system for atmospheric monitoring, fire and dust suppression systems, power supplies/battery back-up, fans and airflow systems.
Harrington Hoists offers a broad range of hoists used for gold mining, including overhead cranes, crane accessories, chain hoists and trolleys, electric wire rope hoists and trolleys, lever hoists, manual hand chain hoists, push and geared trolleys, and a full line of replacement parts.
MSA safety solutions are used at gold mining sites across the globe. Its safety equipment includes the Altair 4X Detector, a portable multi-gas detector that can alert the user to the presence of combustibles, toxins, and anaerobic environments in 15 seconds, as well as the W65 Self-Rescuer Respirator, a one-time-use device that provides emergency respiratory protection against carbon monoxide.
Page Boss phones provide clear and undistorted communication for an entire gold mining network, the company’s portfolio of phones can be mixed and matched to build a complete communication system above or below ground.
The best way for Carroll Technologies to provide gold mining equipment for your mine is through a consultation to meet your site’s specific needs. Book a free safety consultation here or call 606-573-1000 to find out more.