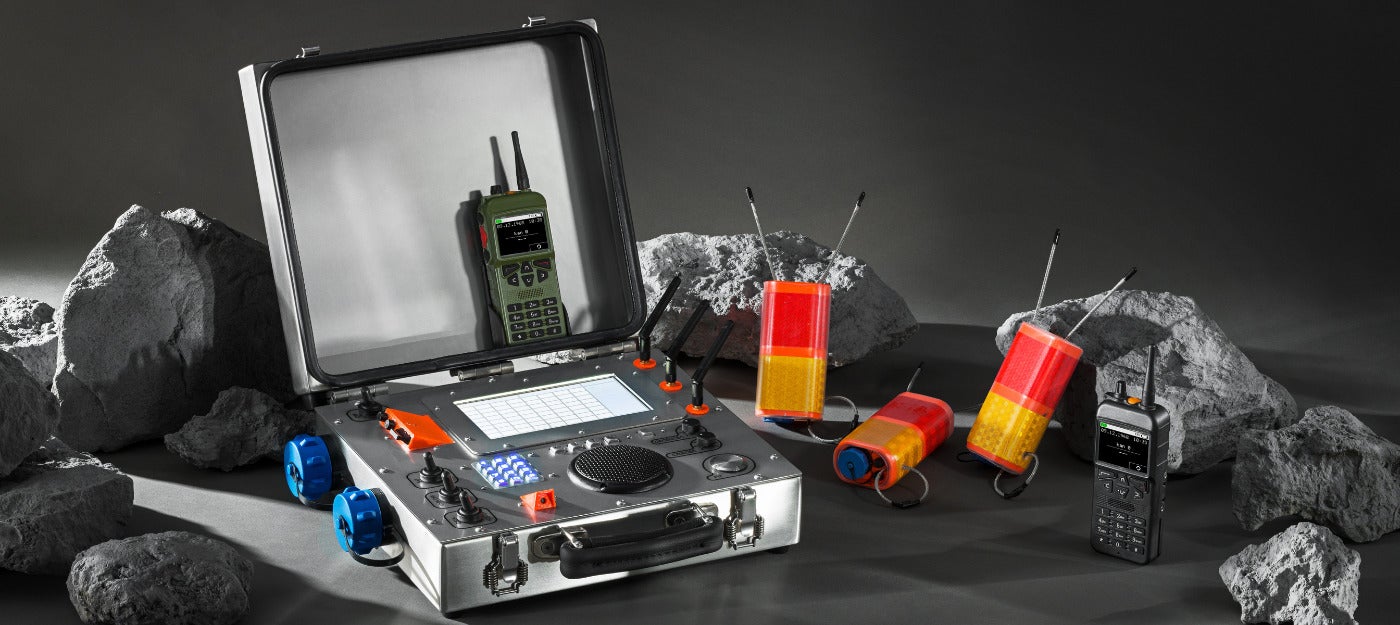
From mines and tunnels to trenchless construction sites and emergency rescue operations, Sybet’s portable communications systems enable secure, wireless voice communication and tracking without the need for pre-installed infrastructure. Whether you’re conducting routine maintenance or responding to a life-threatening incident, Sybet systems are engineered to deliver fast deployment, extended operational time, and absolute reliability.
Why Portable Underground Communications Systems Matter
In underground worksites, especially during rescue operations, there is no time to waste installing cables or permanent communication lines. Immediate communication between underground teams and the surface is essential not just for efficiency, but for survival.
Sybet systems are uniquely suited for:
- Mine rescue operations
- Tunnel maintenance and exploration
- Trenchless and utility construction
- Cave or viaduct inspections
- Any scenario lacking fixed underground-to-surface infrastructure
Their plug-and-play design and battery-powered nodes enable rapid setup in even the most challenging environments.
Tailored Communications Systems for Different Underground Challenges
Sybet offers several advanced systems, each suited for different underground applications:
SWAR-2EX System
Designed for mine rescue and emergency response, the SWAR-2EX creates a temporary wireless communication network using a series of portable battery radio nodes and radiotelephones. It supports voice communication, position tracking, and network health monitoring. A fully charged node can operate for up to five days, providing uninterrupted connectivity during long-duration missions.
SpellCom System
Ideal for cave systems, dam inspections, or other confined underground spaces, SpellCom uses compact MiniNodes to create a scalable radio network. It supports localization, phone tracking, battery-level monitoring, and can be expanded to suit both small-scale and large-scale deployments.
With support for ATEX and IECEx-certified devices, Sybet systems meet international safety standards for explosive atmospheres, making them a trusted choice for hazardous mining environments.
Every Rescue Team Should Be Equipped
Communication is the backbone of any rescue effort. In situations where lives are on the line and infrastructure is damaged or absent, Sybet systems provide the only portable communication solution capable of linking underground personnel with surface teams in real-time. Deploying a Sybet network can be the difference between delay and rescue.
That’s why every mine rescue team should have immediate access to a Sybet system and a sufficient number of nodes, ready for deployment whenever an emergency arises.
See the Sybet System in Action
Experience the rapid deployment and operational efficiency of Sybet’s portable communication systems through the following demonstration. This video showcases the placement of Sybet nodes within a tunnel environment, highlighting the system’s ease of setup and robust performance in underground conditions.
This visual demonstration underscores the practical benefits of Sybet’s technology, particularly in scenarios where immediate and reliable underground communication is critical.
Your Trusted Supplier: Carroll Technologies Group
As a leading provider of mine safety and communications equipment in North America, Carroll Technologies Group is proud to be the exclusive supplier of Sybet portable communication systems across the US and Canada.
We don’t just provide the products, we offer:
- Expert consultation to choose the right Sybet system for your needs
- Full installation and setup support
- 24/7 post-purchase technical assistance through MinerCare™
- Servicing and repair to keep your systems running smoothly
Whether you need a portable system for a single site or are equipping multiple rescue teams across a region, Carroll Technologies has the experience, inventory, and support network to deliver.
Get in Touch
To learn more about Sybet systems or to discuss your site’s specific communication needs, contact Carroll Technologies today. Our experts are here to help you build safer, smarter underground operations – without compromise.