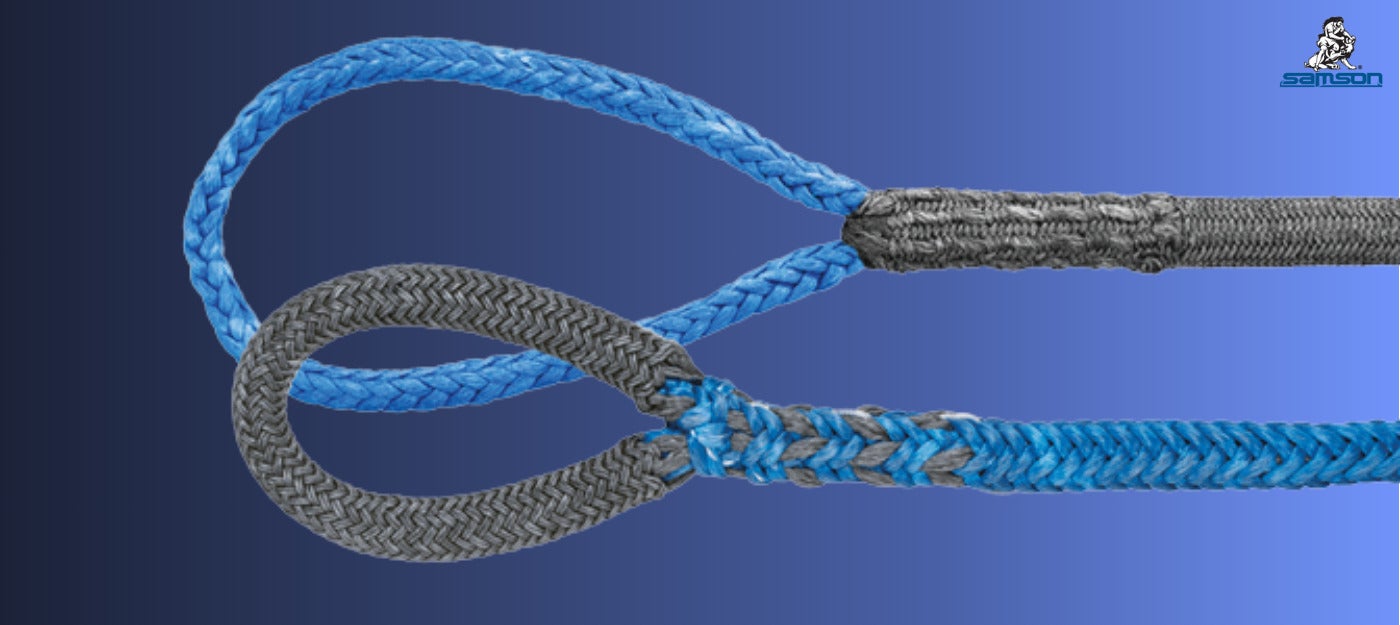
The Evolution of Industrial Rope: Strength Meets Innovation
Traditional rope materials, including natural fibers and steel wire, have long been used in industrial applications. However, these materials come with significant limitations. Natural fiber ropes degrade quickly when exposed to moisture and UV rays, while steel wire ropes, though strong, are heavy, prone to corrosion, and require extensive maintenance.
Innovative synthetic rope technology has proven to be a game-changer, overcoming these limitations. Synthetic ropes, particularly those made from high-performance fibers such as Dyneema®, offer the perfect balance of strength, lightweight construction, and longevity. Unlike steel wire, synthetic ropes are easier to handle, which reduces strain on workers and improves overall safety.
Samson Rope: Pioneering the Future of Industrial Ropes
Samson Rope has built its reputation on relentless research and development, consistently introducing groundbreaking rope solutions that enhance safety and efficiency. These solutions include synthetic ropes designed to handle extreme loads while maintaining flexibility and ease of use. The company’s Dyneema® fiber ropes are up to 15 times stronger than steel by weight, making them ideal for applications where strength and lightweight performance are critical.
One of the most significant advantages of Samson’s synthetic ropes is their reduced weight compared to steel wire ropes. This makes them easier to transport, install, and maneuver, drastically reducing the risk of workplace injuries caused by heavy lifting. Additionally, synthetic ropes do not develop dangerous wire splinters, further improving safety for workers. Furthermore, whether exposed to saltwater, chemicals, or extreme weather, Samson’s ropes are engineered to withstand the most demanding conditions.
Looking Ahead: The Future of Industrial Rope Technology
The future of industrial rope technology lies in continued innovation, and Samson remains at the cutting edge. With advancements in fiber technology, rope coatings, and digital monitoring systems, the next generation of ropes will be even stronger, safer, and smarter.
From reducing carbon footprints with more sustainable materials to integrating smart sensors that provide real-time load data, Samson is driving the evolution of industrial rope solutions. By investing in research and development, the company ensures that industries relying on rope technology will continue to benefit from lighter, stronger, and more resilient solutions.